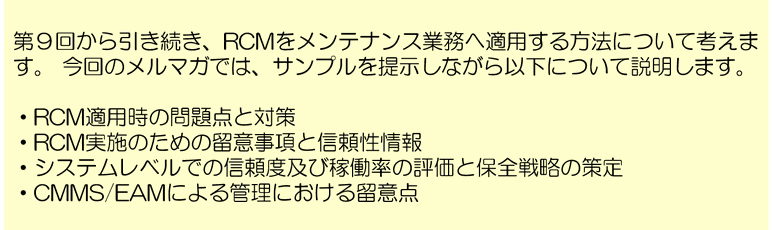
1.信頼性中心保全(RCM:Reliability Centered Maintenance)
第9回のメルマガでは、信頼性中心保全(RCM)とCMMS/EAMの関係を示しました。
前稿では、着目するコンポーネントの機能と機能喪失を定義し、 その故障モード(または原
因)を列挙した後、各故障モードに対する対策を検討する方式を説明しました。 本方式は、信
頼性中心保全(RCM)と呼ばれ、FMEAやFMECAをベースにした考え方です。
RCMでは、コンポーネントや機能の列挙、故障モードの列挙を全て実施し、 故障モードによる
影響やリスクを排除または許容できるレベルに抑えるための 対策の検討や評価を行い、保全方
式や戦略を決定します。
2.RCM適用時の問題点と対策
ところが、ここで、問題が発生します。
・検討量が膨大.
コンポーネントの列挙、故障モードの列挙等から対策の検討まで、どれだけの検討と評価 を行う必要があるのか。
・コンポーネントに対して故障モードを全て列挙することは困難.
故障モードは列挙したが、コンポーネントごとに多数存在し、 どこまで、検討すればよい
のか。
・リソースが準備できない.
自社のリソースだけでなく、外部の専門家も必要となり、リソース(人員、費用)は、 ど
れだけ必要になるのか見積もれない。
特に、すでにプラントが稼働している場合、 「実際には、RCMの様な評価を行わなくても、プ
ラントは、正常に稼働しています。 効率は悪いかもしれませんが…」という疑問も発生します。
・高い信頼性や安全性を確保したいシステムに対して、RCMを適用したらどうだろうか?
・特に不適合や故障が頻発しているところに、RCMの様な考え方を導入することで、
信頼性を上げることができないだろうか?
・稼働率を高めるためには、どうすれば良いのだろうか?
・そもそも、稼働率を高めることと、信頼性を確保することは、同じこと、それとも、異なる
もの?
・RCMを導入する場合、はたして、有効性はどうだろうか?
以上の様な「RCMをゼロベースで実施するためには、 大量のリソースが必要」に対する処置とし
て、最近では、RCMのエッセンスを残しつつ、 検討・評価の労力を軽減する手法も提唱されて
います。
問題点の対策のひとつとして、CMMS/EAMとRCMを連携した運用を行うことが考えられます。 CMMS/EAMとRCMの連携により、以下の効果が期待できます。
・設備台帳として機器のリストが揃っており、RCMの機能リストの初期値として利用可能
・故障や不適合に関する情報の管理が可能
・故障を分析することにより、保全方式の選択や周期の適正化の評価に役立てることが可能です。
・TBMやCBMの計画化、実施管理が可能
RCMに基づく保全戦略の策定では、TBMやCBMなどの保全方式の検討、保全項目や周期の検討を行います。 これらの初期値としてCMMS/EAMに登録された内容が活用でき、検討結果を反映することが可能となります。
但し、CMMS/EAMとRCMを連携して用いるためには、設備台帳の粒度や故障情報の内容について違いを留意する必要があります。
本メルマガでは、CMMS/EAMとRCMを連携して用いることを考えるために、 RCMのベースとなっている信頼性情報や信頼性評価の解説も交え、以下を説明します。
・RCM実施のための留意事項と信頼性情報
・システムレベルでの信頼度及び稼働率推定と保全戦略の策定
・CMMS/EAMによる管理の留意点
3.RCM実施のための留意事項と信頼性情報
RCMを適用する当たり、どこに対して適用するのか、 そして選択した対象の信頼度は、どうあるべきなのかを考える必要があります。 どうあるべきかを考えるためには、故障とは何か。 故障するとシステムはどうなるのかを考える必要があります。 RCMのベースとなっている信頼性評価の世界では、これらを定量的に扱うために、 故障率、信頼度(不信頼度)、稼働率(不稼働率)を用います。
特に、故障率と信頼度の関係は重要です。 プラントや機器の設計段階でも信頼度を評価するために故障率を用いますが、 この場合、通常は、平均値を用います。 これに対して、保全の世界では、故障率の平均値を用いても、 最適な計画を策定することはできません。 故障率は、時間に依存します。 とくに摩耗故障を起こす機器の場合、時間とともに、信頼度は加速度的に悪くなります。 ということは、故障率の特性(機器の壊れ方・癖)を知る必要があります。
故障率と信頼性情報の関係は、以下ページを参照して下さい。
参照(A)の説明の中で示した様に、ある機器の故障数(頻度)が判れば、 故障率、信頼度(不信頼度)の一式が判ります。 通常は、機器仕様(機種)、環境、そして、使用頻度などが同じと見なせる機器の 故障情報を集めて集計することで、故障率や他の信頼性情報を計算します。 もし、故障情報が入手できる場合は、集計の方法として、ワイブル分析が良く使われます。
ワイブル分析の説明は、このページを参照して下さい。
参照(B)で示したように、ワイブル分析は、時間依存の不信頼度(故障率)を故障情報から近似することができます。 また、ワイブル分析では、故障情報が存在しない場合に対する方法も提案されています。 これに対して、FMEA/FMECA(※1)のみを用いる場合、故障モードに対するリスクの評価は、RPN(※2)のみを用いるため、 影響度や致命度は、判りますが、いつ不信頼度が増加するのかが判りません。 このことは、FMEA/FMECAのみの場合、リスク(RPN)は、判るが、保全周期の決定には困難を伴うことを意味します。 なお、リスク(RPN)が高い場合は、リスクを排除すために実施すべきこと(戦略)を検討する必要があります。 この戦略の中で出てきた保全項目をどれ位の頻度で実施すれば良いかを検討するために ワイブル分析結果等の故障分析結果が活用できます。
※1 FME(C)A:故障モードと影響(及び致命度)分析
※2 RPN:リスクプライオリティナンバー
リスクを致命度x頻度x検知のし易さとして評価した値であり、時間依存性はない。
4.システムレベルでの信頼度及び稼働率の評価と保全戦略の策定
次に、機器の故障がシステムに与える影響を考えます。 機器の癖(故障率)が判ったとして、
これらの機器を組み合わせて構成されたシステムの不信頼度(故障率)を 知ることで、システ
ムの特性を知ることが出来ます。 システムの故障に対する特性は、信頼度を評価することで推
定できます。 システムの信頼度を知る方法には、RBD(※3)やFTA(※4)が存在します。
※3 RBD:Reliability Block Diagram(信頼性ブロック図)
※4 FTA:Fault Tree Analysis(フォルトツリー分析)
システムに対する信頼性評価の例として、簡単なシステムを例にRBDを用いた 評価を示しま
す。システムに対する信頼性評価の例は、以下を参照して下さい。
システムの信頼度を向上させるための手段としては、不信頼度(故障率)の成長を考慮して、
保全計画を立てることになります。
システムを構成する機器の不信頼度が判っていれば、 機器ごとに何回に1回の頻度で保全を実
施すれば良いか等の目安も立てられます (B-Life指標値の活用:「故障率と信頼性情報の関係」を
参照)。
故障率に摩耗故障領域が存在する場合は、 「不信頼度が急激に成長する前に定期的に更新工事
を実施する」などの 計画が有効になります(TBM※5)。
また、環境や使用頻度が変わる場合もあるため、 定期的な検査を実施し、機器の健全性を考慮
した上での更新計画策定も必要でしょう(RBIやRBM※6)。
故障率が偶発故障のみの場合は、検査やモニタリングが有効な手段となります(CBM※7)。
※5 TBM:Time Based Maintenance(時間基準保全)
※6 RBI(M):Risk Based Inspection(Maintenance)(リスク基準検査(保全))
※7 CBM:Condition Based Maintenance(状態基準保全)
上記に基づき保全方式を検討した後、 保全の効果を推定する場合には、ライフタイム全般にわ
たる稼働率を考える必要があります。 稼働率は、信頼度に保全計画を含めることで、推定でき
ます。 信頼性評価の世界で考えると、保全を実施するということは、成長した不信頼度をリセ
ット(※8)することを意味しています。
※8 厳密には、完全にリセットできるのか、50%程度をリセットできるのかなどを考慮する
必要があります。
以下に、信頼性評価に保全計画を組み合わせた場合の稼働率推定の例を示します。 稼働率推定
の例は、以下を参照して下さい。
5.CMMS/EAMによる管理における留意点
前節では、不信頼度(故障率)を用いたシステムの信頼度や稼働率の推定例 を示しました。
では、前節の様な信頼性評価を踏まえた上で RCMを適用していくためには、 CMMS/EAM
でどの様な管理を行えば良いでしょうか。 以下に留意点を列挙します。
・機器をシステムや系・系統で集約できる様な体系を考慮
機器の不適合や故障を集計する場合、機器仕様、環境、使用頻度(負荷)等で 集計する必
要があります。 環境や使用頻度を考える場合、機器が属するシステムや系・系統で扱える
と 集計が簡単になります。 保全の立場から考えると、系や系統による機器のくくりは、
損傷要因をグループ化する効果があります。
例えば、異なる系や系統に同じ仕様を持つポンプが設置されているとしても、 中を流れる
流体が水と油の様に異なる場合、壊れ方も異なります。 さらに、管理方法も異なります。
・管理の粒度の検討
RCMの様に故障の要因や原因に基づく管理を行う場合、 機器をどのレベルで管理するか
が重要となります。 機器のレベルは、CMMS/EAMの設備台帳に何を登録するかに直結
します。
厳密には、故障モードに関連したレベルでの登録が望ましいですが、 保全管理を実施する
場合、故障モードに関連したレベルでは、細かすぎて、 保全の管理ができません。
故障モードに関連したレベルは、機器の部位・部品レベルとなる可能性が高いからです。
故障分析を行う場合(不適合や故障を集計する場合)は、故障情報のグループ化のために
原因や部位・部品が判別できれば良いので、 設備台帳に登録するレベルは、保全計画時の
最小管理対象や取り換え可能部品(RU:Replaceable Unit)などの保全単位レベルで 管理
すると良いと考えられます。部位・部品は、設備台帳の付帯情報として管理し、不適合や
故障時の原因として報告できれば、良いでしょう。
・検査や保全の効果の明確化
RCMの観点から検査を考えると、検査は、 機器の特定の故障モードの進展状況を検知ま
たは捕捉することにあります。
機器には、多数の故障モードが存在し、検査は、どの故障モードを対象とするのか、 ま
た、検知や捕捉ができない故障モードは何かが重要となります。
保全の立場で言い換えると、故障の要因に着目した検査の計画策定が重要になりま
す。
CMMS/EAMで検査を管理する場合、検査が対象としている要因(どの故障モードに対応
するのか)を併せて管理しておくことが重要です。そうすることで、不幸にして故障等が
発生した場合、是正処置実施時に、要因に立ち返り検査実施内容を検討することができま
す(≒RCMの考え方に基づいて、再検討が可能となる)。
保全の実施も同様です。保全の実施により、どの故障モードが対象となるのかが重要とな
ります。信頼性評価の立場から考えると、不信頼度がどの程度リセットされるのかに関係
してきます。
・工事・発注単位の考慮
CMMS/EAMで保全管理を実施する場合、本稿で考えているRCMに基づく管理とは、別
の管理が存在します。
検査や保全(工事)を具体的に計画する場合、工事や発注の単位は、本稿で述べている単
位ではなく、 プラント全体、装置、系・系統一式、機種の一式、ベンダー別など大きなく
くりになります。 個々の機器についての計画は、要因をもとに考える必要がありますが、
工事や発注は、 グループ化して考える必要があります。 また、グループ化する過程で、
「要因ベースで考える場合は、次回の工事の中で実施する」で良いが、 「工事の都合で、今
回に含めたい」等の調整が可能である必要があります。
・前回の修理(や設置・更新)からの時間が明確になる様な管理
CMMS/EAMに記録された不適合や故障情報を用いて、不信頼度(故障率)の定量評価
(故障分析)を行う場合、 発生頻度(横軸時間、縦軸件数等)が重要な情報になります。
発生頻度を求めるためには、前回の修理(や設置・更新)から不適合や故障発生までの時
間が必要となります。 本情報があれば、ワイブル分析も簡便に実施することが出来ます。
また、不信頼度(故障率)をワイブル分析で求める場合、故障していない機器の情報を加
味することで、 現実に沿った値を計算することができます。 よって、故障をしていない
機器についても、前回の修理(や設置・更新)時期情報を管理する必要があります。
本情報は、CMMS/EAM導入時に考えられていない場合が多く、 後から履歴をさかのぼ
り集計処理を行うのは煩雑な処理になる可能性が高いため、留意が必要です。
6.最後に
今回のメルマガでは、RCMと保全周期の評価、それを実施するためのCMMS/EAMでの留意点について検討しました。 広範囲の内容を1回のメルマガでまとめたため、判りにくい点もあると思います。 本稿で述べた内容については、定期的に無料セミナーを開催していますので、こちらもご活用ください。
信頼性解析ソフトウェアの活用セミナー
保全システム紹介セミナー:
点検(保全)周期表をベースにした保全管理システム紹介セミナー
「FLiPS」「AiPOST」
前 「第9回:信頼性中心保全(RCM)とCMMS/EAMの関係」
第11回以降は作成中です。
※更新のお知らせをご希望の方は下記お問い合わせフォームよりご登録ください。
<お問い合わせフォーム>
● お問合せ先
株式会社ウェーブフロント
営業部
メール:sales@wavefront.co.jp
TEL:045-682-7070